Largest Small Heart Manufacturer in the US
In 1855 in New Orleans, Christopher Henry Miller turned his pastry chef experience into the Miller Candy Corporation. His son-in-law, Augustus Elmer, eventually joined him. Around the turn of the century, the company’s name was changed to Elmer-Miller. In 1914, Elmer’s sons signed on to what is now known as Elmer Candy Corporation.
Elmer is currently the second largest heart box manufacturer in the country with products distributed to more than 100 retailers in 13 different countries. Easter favorites Gold Brick®, Heavenly Hash and Pecan Eggs outsell national leaders five to one along the Gulf Coast.
Maintaining Training Excellence
In-house training
Elmer Chocolate was one of our first customers when we started out in 2016. The Food Safety Modernization Act (FSMA) was in its roll-out phase and they needed to get several employees trained to become PCQIs (Preventive Controls Qualified Individuals) so they could develop their food safety plans to comply with the new FSMA regulations.
Sending several employees to a public class can be costly and is oftentimes more cost effective to have team members trained in-house. They also wanted to customize the training as much as possible to focus on their product category, chocolate confections.
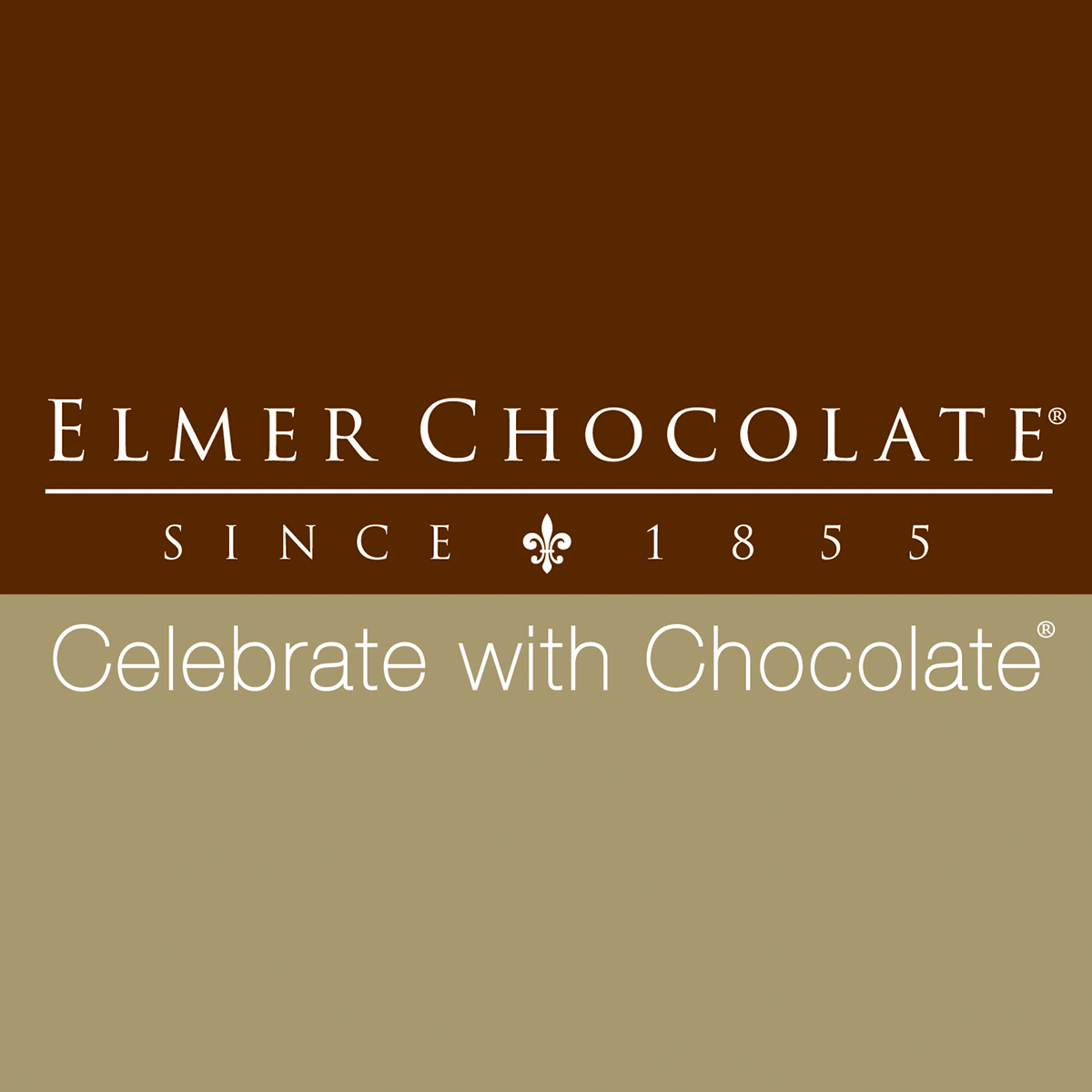
Food Safety and Quality Services created a cost-effective training program and delivered a customized training experience for their employees.
We can customize our training approach
Using “real-life” scenarios keeps trainees engaged
Food Safety and Quality Services created a cost-effective training program and delivered a customized training experience for their employees. Since then, we have continued to train Elmer employees in our public classes as well as onsite at their facility. Elmer recently asked us to develop a customized root cause analysis and corrective action training for their employees. We worked together to develop a personalized training agenda that fit their needs. By utilizing their actual programs, procedures and “real-life” scenarios in the training, their employees stayed engaged and were able to work together to restructure their approach to root cause analysis and develop a more sustainable program.
Need a Food Safety Specialist?
Free 15 Minute Consultation.upcoming Classes
September 17, 2025 09:00 AM - 03:00 PM
October 14, 2025 08:00 AM - October 16, 2025 05:00 PM
August 26, 2025 08:00 AM - August 28, 2025 05:00 PM